FDA Observations Audit Management
1. Missing Quality Audits
Root Cause:
Lack of internal audit schedule, inadequate adherence to QMS procedures, understaffing, and oversight of audit activities.
Corrective Action:
Develop a documented internal audit schedule, conduct immediate audits, train additional personnel, and revise SOPs to emphasize internal audits.
Preventive Action:
Regularly train staff on audits, establish a reminder system, implement CAPA for audit findings, and update the audit schedule and procedures regularly.
Reference FDA 483:
Company Name: Theranos, Inc.
Issue Date: 16-Sep-15
Inspection Dates: 25 Aug 2015 to 16 Sep 2015
Investigators: Mary R Hole, Yung W Chan, Lawrence Farina
2. Equipment Design Does Not Facilitate Intended Use
Root Cause:
No internal audit schedule, inadequate quality oversight, and insufficient resources for audits.
Corrective Action:
Develop a comprehensive audit schedule, allocate resources, and mandate training on the importance of audits.
Preventive Action:
Prioritize audits in the QMS, incorporate audits into performance metrics, and regularly update the audit schedule based on changes and findings.
Reference FDA 483:
Company Name: Chen Shwezin, Inc. dba Park Compounding
Issue Date: 11-Sep-15
Inspection Dates: 31 Aug 2015 to 11 Sep 2015
Investigators: Liming Zhang, Darren S Brown, Lawrence Farina
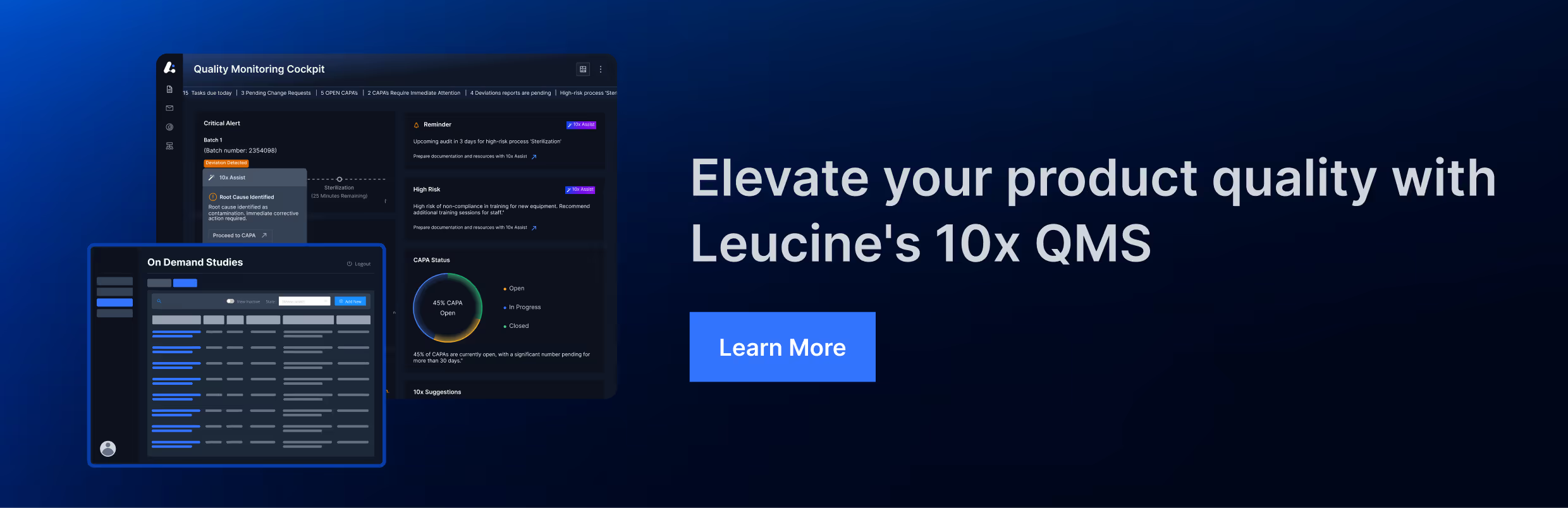
3. Inadequate Specifications for Components
Root Cause:
Lack of robust audit scheduling, oversight, and prioritization within the QMS.
Corrective Action:
Implement audit management software, allocate resources, and prioritize audits with top management oversight.
Preventive Action:
Form a cross-functional audit committee, integrate audit reviews into senior management meetings, and train employees on the importance of audits.
Reference FDA 483:
Company Name: Wood's Pharmacy, Inc., dba The Medicine Shoppe
Issue Date: 15-Jan-15
Inspection Dates: 12 Jan 2015 to 15 Jan 2015
Investigators: Tajah L Blackburn, Nebil A Oume
4. Inadequate Maintenance of Equipment and Utensils
Root Cause:
Lack of CAPA procedures for level 3 investigations, insufficient regulatory understanding, inadequate training, absence of tracking tools, and poor management commitment.
Corrective Action:
Develop CAPA procedures, train personnel, institute a tracking system, and conduct management reviews to reinforce compliance.
Preventive Action:
Regular audits, mandatory management reviews, and continuous training on regulatory requirements and procedures for level 3 investigations.
Reference FDA 483:
Company Name: Downing Labs, LLC
Issue Date: 16-Jul-14
Inspection Dates: 03 Jun 2014 to 16 Jul 2014
Investigators: Stephen D Brown, Darla J Christensen
5. Inadequate Establishment of Quality Audit Procedures
Root Cause:
Lack of detailed audit planning, insufficient audit scope and frequency, and inadequate coverage of quality systems.
Corrective Action:
Revise audit procedures, implement a detailed schedule, and train audit personnel.
Preventive Action:
Regularly review and update audit procedures, audit the audit process for improvement, and enhance training on strategic planning and scope definition.
Reference FDA 483:
Company Name: Hospira, Inc.
Issue Date: 17-Jun-11
Inspection Dates: 16 May 2011 to 17 Jun 2011
Investigators: Jason F Chancey, Penny H McCarver
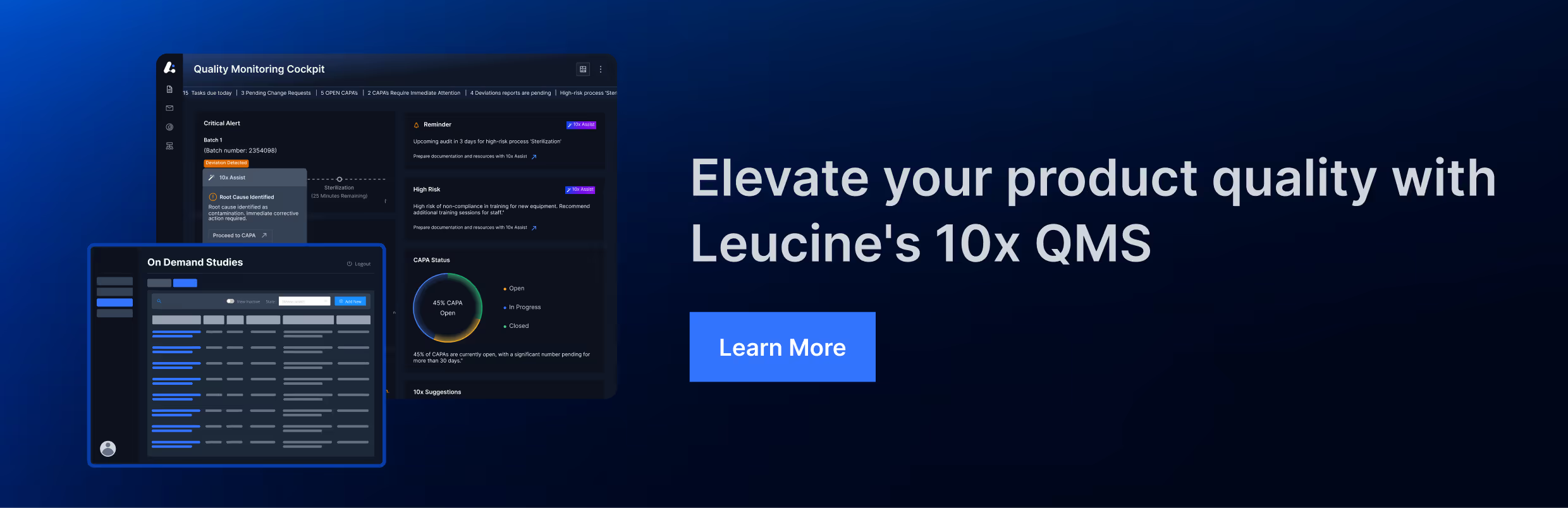
6. Lack of SOP and Documented Procedures
Root Cause:
No SOPs for vendor qualification, lack of regulatory understanding, inadequate resource allocation, and miscommunication on vendor qualification importance.
Corrective Action:
Develop and implement SOPs for vendor qualification, allocate resources, audit current vendors, update QMS, and consult regulatory experts.
Preventive Action:
Establish continuous training, periodically review SOPs, implement a vendor management system, and promote a culture of quality and compliance.
Reference FDA 483:
Company Name: Time Cap Labs, Inc.
Issue Date: 05-May-98
Inspection Dates: 26 Mar 1998 to 05 May 1998
Investigators: Lawrence Farina, Robert C Horan
Dive Deep into the Following Critical Aspects
Ensure all records are complete, accurate, and easily accessible.
Evaluate the efficiency and effectiveness of your processes and systems.
Verify adherence to all relevant regulations and standards.
Assess the condition of your facilities and the competence of your staff.
Check the effectiveness of internal and external communication channels.
Ensure ongoing tracking and resolution of CAPAs to maintain compliance.

.png)
.png)
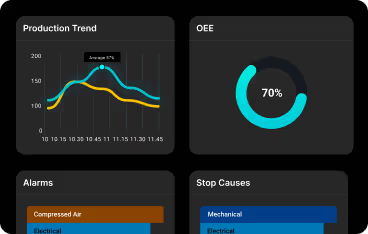
.png)