Common Blend Residue Limit
Learn practical methods for calculating cleaning limits for equipment handling common blends in pharma, ensuring compliance with FDA cleaning validation rules
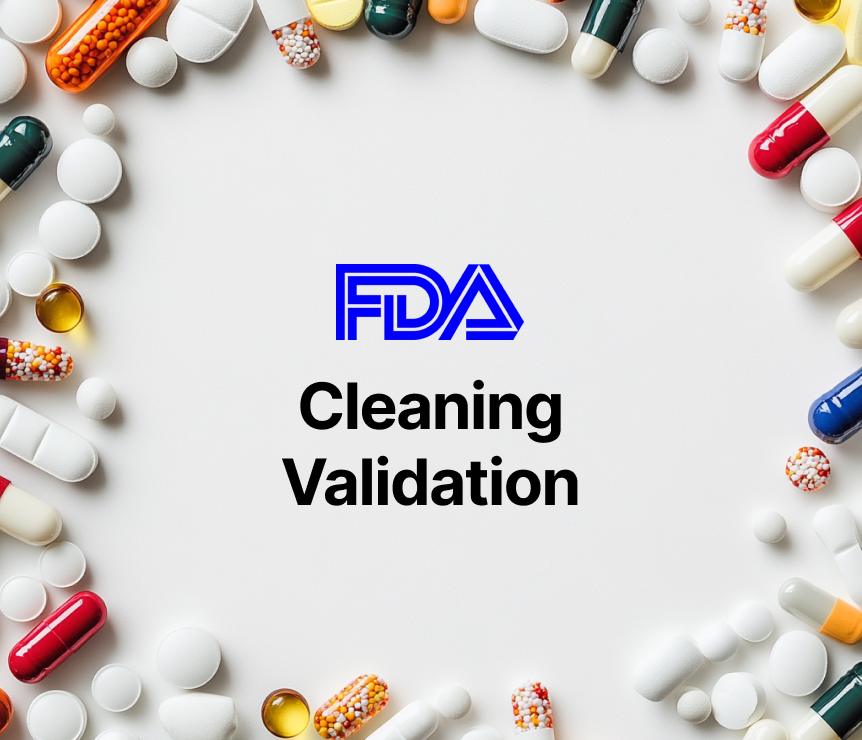
Managing the residues of common blends across various production lines is a challenge laden with complexity yet critical for ensuring product safety and regulatory compliance. This guide explores the practical methodologies for calculating cleaning limits for equipment handling common blends, tailored specifically for pharmaceutical manufacturing professionals.
Understanding the Challenge of Common Blends
Common blends, utilized across different product lines, introduce unique challenges in residue management due to their use in producing multiple product strengths. Consider a scenario where a 100 kg common blend is divided among three distinct lines to produce different strengths: Product A (40 mg), Product B (50 mg), and Product C (10 mg). Each line employs a different set of equipment, which in turn can come into contact with various subsequent products. The divergence in equipment trains necessitates a meticulous approach to calculating cleaning limits to prevent cross-contamination and ensure the integrity of each manufactured product.
Strategic Approach to Calculating Cleaning Limits
The cornerstone of managing common blend residues lies in addressing the equipment's cleaning limits tailored to the specific needs of each product derived from the blend. The process entails several critical steps:
Segregation and Individual Assessment
Initially, each product resulting from the common blend must be individually assessed. This means treating Products A, B, and C as separate entities for the purpose of residue limit calculation. The unique characteristics of each product, such as potency and toxicity, necessitate this individualized approach to accurately determine the cleaning limits required for each product line. This step ensures that specific risks associated with each product are adequately addressed.
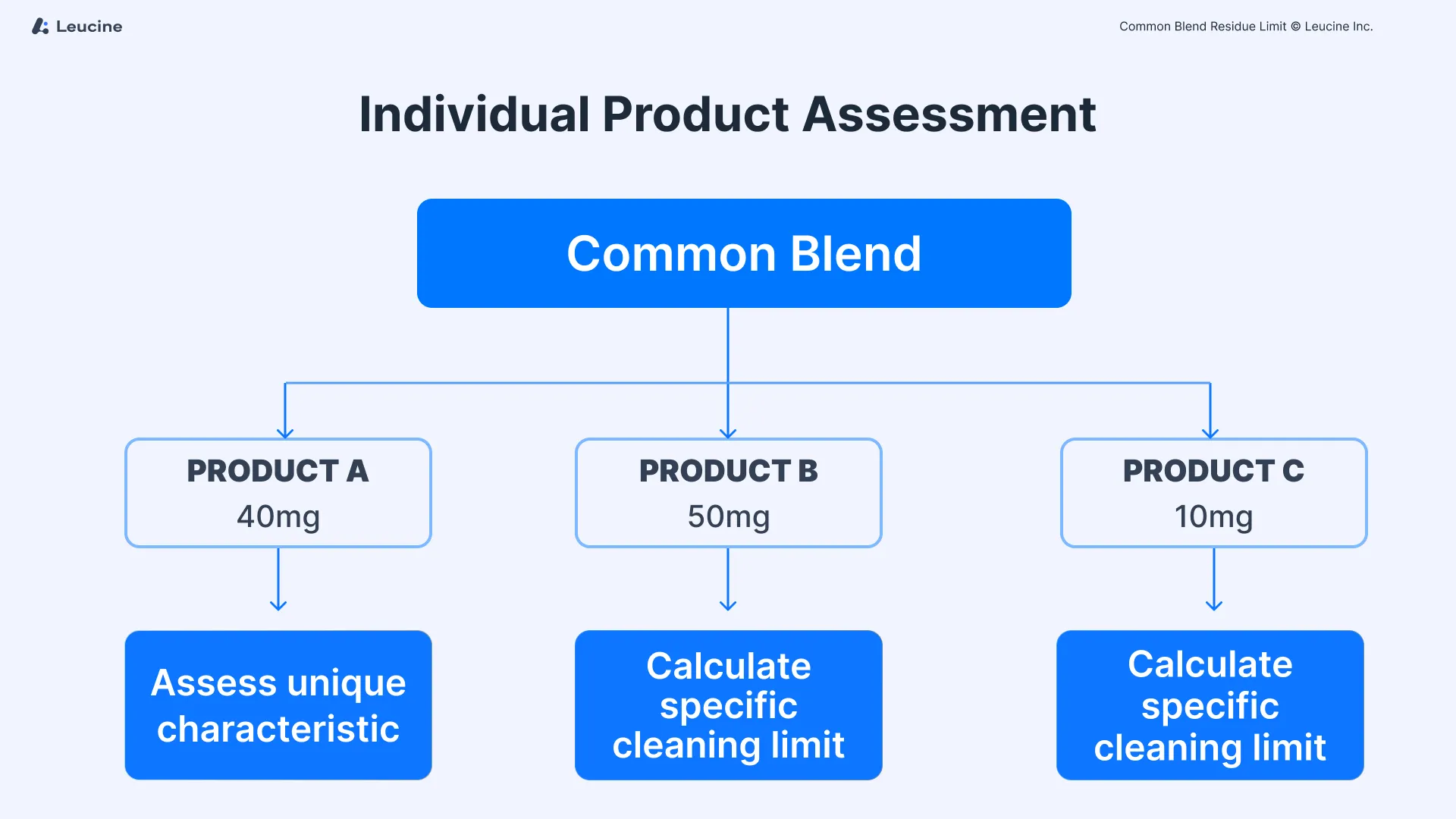
Evaluation of Cross-Contamination Potential
The next crucial step involves evaluating the potential for cross-contamination among the products derived from the common blend. This involves a detailed analysis of the manufacturing process, particularly focusing on the shared equipment train. By identifying which pieces of equipment are utilized across different production lines, manufacturers can pinpoint where residues might be transferred between products. Understanding these cross-contact points is essential for determining where and how stringent cleaning protocols need to be applied.
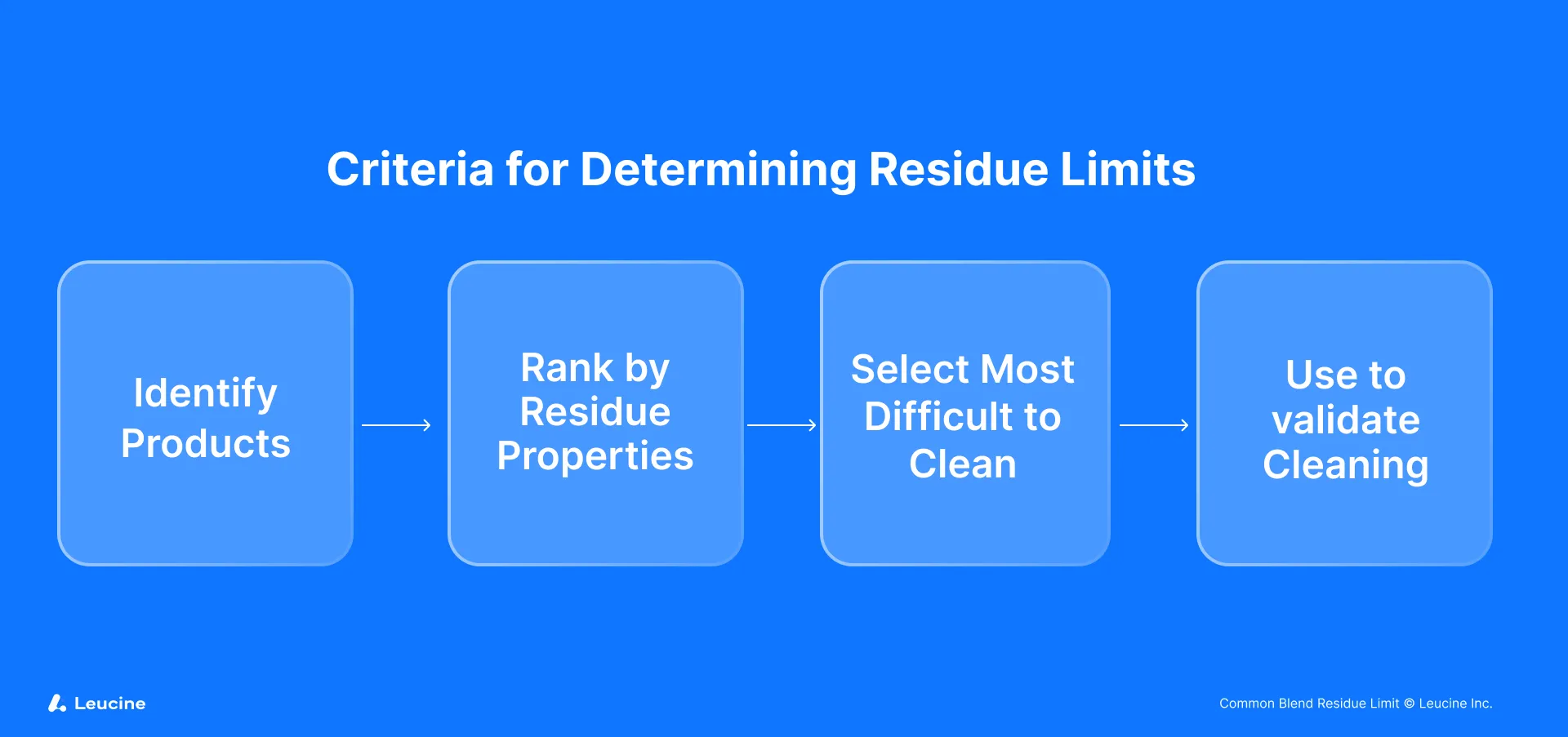
Comprehensive Surface Area Analysis
Following the identification of shared equipment, a comprehensive analysis of the total surface area exposed to the common blend is required. This involves calculating the surface area of each piece of equipment that comes into contact with the blend during the manufacturing process. The total surface area calculation is critical as it directly influences the residue limit for each product. Larger surface areas may require more stringent cleaning limits due to the greater potential for residue accumulation and transfer.
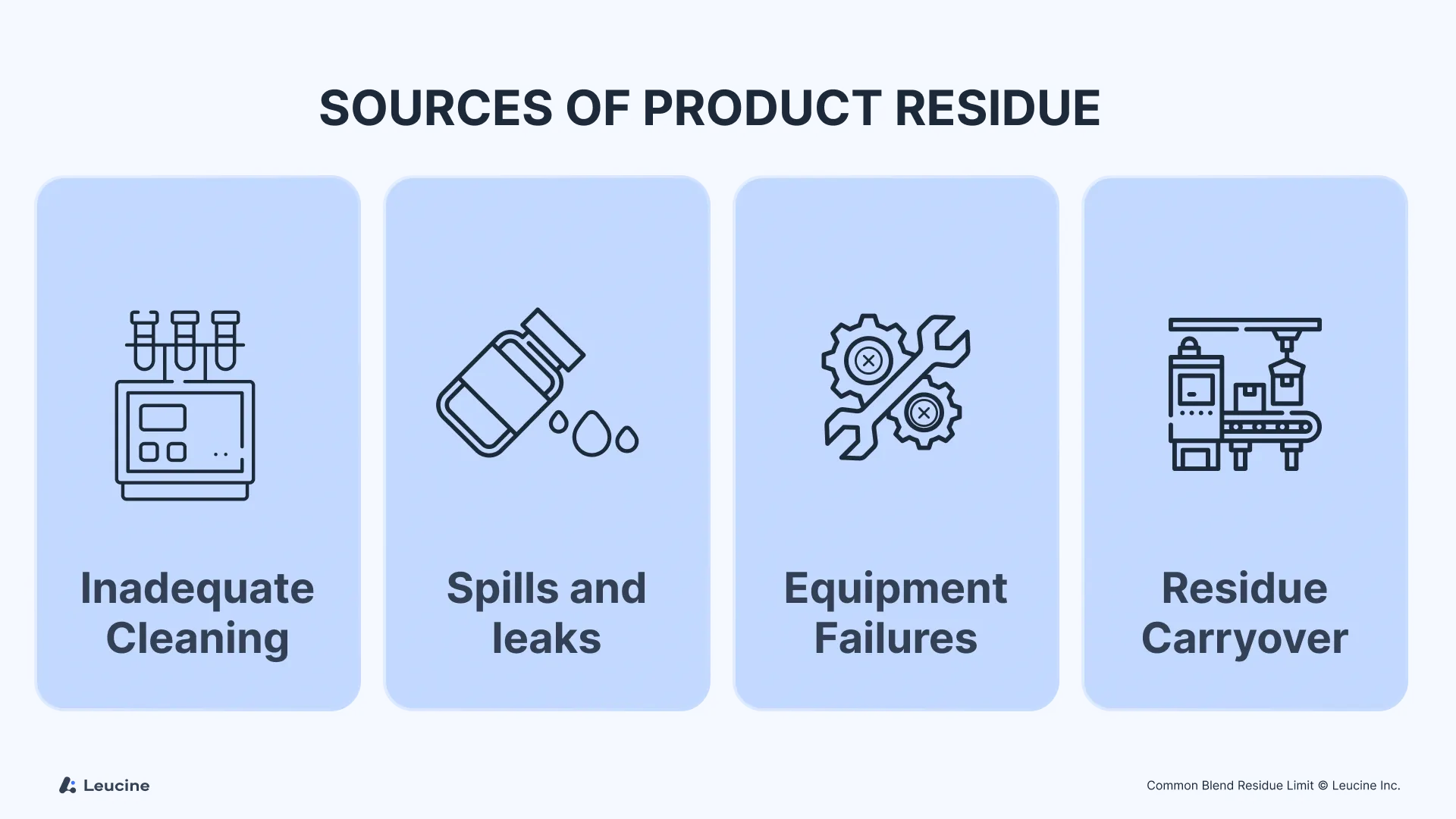
Calculation of Cleaning Limits for Each Product
With the shared surface areas identified, the next step is to calculate the specific cleaning limits for each product (A, B, and C) considering all possible subsequent products they may encounter. This involves determining the maximum allowable residue levels on the equipment surfaces to prevent cross-contamination between product batches. The calculation of these limits typically involves toxicological data, product dosage forms, and the therapeutic index, among other factors. The aim is to establish the safest possible threshold for residue levels that ensures patient safety without compromising product efficacy.
Establishing the Lowest Acceptable Limits
After calculating individual cleaning limits, the lowest limit among all evaluated scenarios dictates the cleaning standard for the common blend equipment. This conservative approach ensures that the strictest residue limit is applied, minimizing the risk of cross-contamination and ensuring that all products derived from the common blend meet safety standards.
Worst Case Product Selection
The process culminates in the selection of the worst-case product scenario, typically the product with the highest dosage strength, as it presents the highest risk of significant residue. In our example, Product B, with the highest strength, is considered the worst-case scenario. Establishing cleaning limits based on this worst-case scenario ensures that all products meet the most stringent cleaning requirements, thereby upholding product safety and regulatory compliance.
The methodology outlined for calculating cleaning limits in the context of common blends addresses the nuanced challenges faced by pharmaceutical manufacturers. By systematically evaluating individual products, conducting thorough surface area analyses, and adhering to stringent worst-case acceptance criteria, manufacturers can effectively manage the risks associated with common blend residues. This strategic approach not only ensures compliance with regulatory standards but also upholds the paramount goal of safeguarding patient safety through the production of uncontaminated, high-quality pharmaceutical products.
Streamline validation and scale compliance with Leucine—built for fast-moving pharma teams.
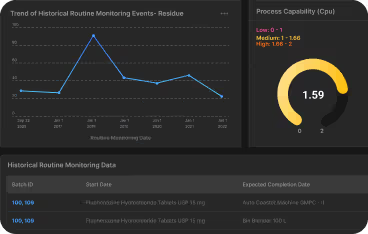
