CAPA Management Guidelines
Discover essential CAPA management guidelines in the pharma industry. Learn best practices, recent changes, and the importance of adherence for continuous improvement.
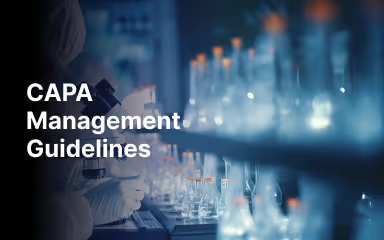
Corrective and Preventive Action (CAPA) management is a fundamental aspect of pharmaceutical manufacturing, playing a critical role in ensuring product quality and regulatory compliance. An effective CAPA system helps pharmaceutical companies identify, investigate, and correct issues, as well as prevent their recurrence. This blog will explore the key guidelines governing CAPA management in the pharmaceutical industry and highlight their importance.
Key CAPA Management Guidelines in the Pharmaceutical Industry
1. ICH Q10: Pharmaceutical Quality System
The International Council for Harmonisation (ICH) Q10 guideline provides a comprehensive model for an effective pharmaceutical quality system, including CAPA management as a critical element. Key aspects include:
- Problem Identification: Detecting and documenting issues that require corrective or preventive actions.
- Root Cause Analysis: Conducting thorough investigations to identify the root cause of issues.
- CAPA Planning and Implementation: Developing and implementing plans to address root causes and prevent recurrence.
- Effectiveness Checks: Monitoring the effectiveness of CAPA to ensure issues are resolved and do not recur.
Useful links: ICH Q10
2. FDA 21 CFR Part 820
The U.S. Food and Drug Administration (FDA) regulations, specifically 21 CFR Part 820, outline the requirements for CAPA in the manufacture of pharmaceutical products. These regulations emphasize:
- Procedures for CAPA: Establishing and maintaining procedures for implementing corrective and preventive actions.
- Analysis of Data: Analyzing data from various sources to identify existing and potential causes of nonconformities.
- Investigation: Investigating the causes of nonconformities and documenting the findings.
- Verification and Validation: Verifying and validating CAPA to ensure they are effective and do not adversely affect the product.
Useful links : FDA 21 CFR Part 820
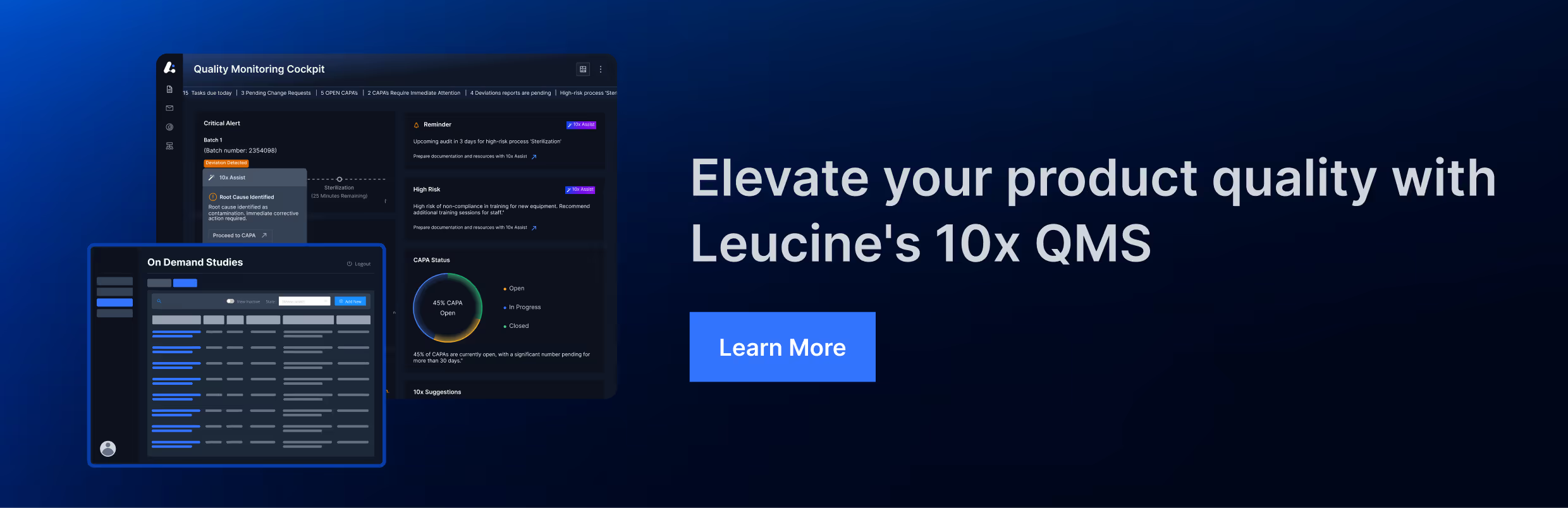
3. ISO 13485:2016
ISO 13485:2016 specifies requirements for a quality management system where an organization needs to demonstrate its ability to provide medical devices and related services that consistently meet customer and applicable regulatory requirements. The standard includes detailed requirements for CAPA management:
- Nonconformity and Corrective Action: Procedures for managing nonconformities and implementing corrective actions.
- Preventive Action: Identifying potential nonconformities and implementing preventive measures.
- Monitoring and Measurement: Tracking CAPA effectiveness through monitoring and measurement.
Useful links: ISO 13485:2016
4. EU GMP Chapter 1
The European Union Good Manufacturing Practice (EU GMP) guidelines, specifically Chapter 1, provide detailed requirements for CAPA management. Key aspects include:
- Quality Management System: Integrating CAPA into the overall quality management system.
- Continuous Improvement: Using CAPA to drive continuous improvement in processes and systems.
- Documentation and Review: Documenting CAPA activities and regularly reviewing their effectiveness.
Useful links : EU GMP Chapter 1
5. WHO GMP
The World Health Organization (WHO) GMP guidelines emphasize the importance of CAPA in maintaining product quality and safety. Key elements include:
- CAPA Procedures: Establishing procedures for implementing CAPA.
- Root Cause Analysis: Conducting thorough investigations to identify the root causes of issues.
- Corrective and Preventive Actions: Implementing actions to address and prevent issues.
- Effectiveness Monitoring: Monitoring the effectiveness of CAPA to ensure issues are resolved.
Useful links: WHO GMP
6. PIC/S GMP
The Pharmaceutical Inspection Co-operation Scheme (PIC/S) GMP guidelines provide a framework for CAPA management to ensure consistency and regulatory compliance. Key aspects include:
- CAPA System: Implementing a system to manage CAPA.
- Data Analysis: Analyzing data to identify trends and areas for improvement.
- Root Cause Analysis and CAPA: Investigating issues and implementing CAPA.
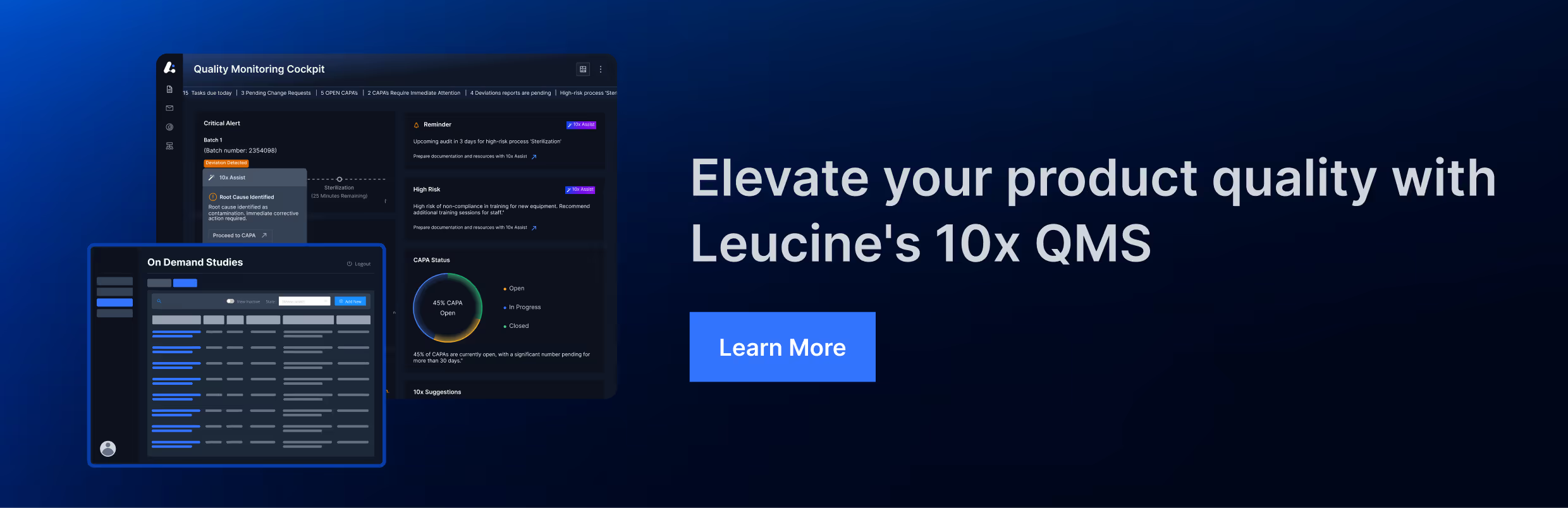
- Documentation and Review: Documenting CAPA activities and reviewing their effectiveness.
The Importance of Adhering to CAPA Management Guidelines
Adhering to CAPA management guidelines is essential for several reasons:
- Regulatory Compliance: Ensures compliance with local and international regulations, avoiding legal issues and penalties.
- Product Quality: Maintains product quality by addressing and preventing issues.
- Risk Management: Identifies and mitigates risks associated with product quality and safety.
- Operational Efficiency: Streamlines processes and reduces disruptions caused by recurring issues.
- Continuous Improvement: Drives continuous improvement of processes and systems, enhancing overall quality.
Best Practices for Effective CAPA Management
To implement an effective CAPA management process, pharmaceutical companies should consider the following best practices:
- Establish Clear Procedures: Develop and maintain comprehensive procedures for CAPA management.
- Train Personnel: Ensure that all relevant personnel are trained in CAPA procedures and root cause analysis.
- Conduct Thorough Investigations: Perform root cause analysis to understand the underlying causes of issues.
- Implement CAPA Plans: Develop and implement corrective and preventive action plans to address and prevent issues.
- Maintain Detailed Documentation: Keep detailed records of CAPA activities, including investigations, action plans, and effectiveness checks.
- Monitor and Review CAPA: Regularly review CAPA activities and monitor their effectiveness to ensure issues are resolved and do not recur.
Recent Changes in CAPA Management Guidelines
Staying updated with recent changes in CAPA management guidelines is crucial for maintaining compliance and ensuring best practices. Here are some recent updates:
1. Revised ICH Q12
The ICH Q12 guideline, which complements ICH Q10, focuses on technical and regulatory considerations for pharmaceutical product lifecycle management. It provides a framework to facilitate the management of post-approval changes, including CAPA processes.
2. FDA's Updated Guidance on CAPA
The FDA has updated its guidance on CAPA to enhance the process of identifying, investigating, and resolving issues. The updated guidance emphasizes the importance of timely documentation and effective root cause analysis to ensure product quality.
3. EU GMP Annex 16 Revision
The European Union has revised Annex 16 of its GMP guidelines to include more detailed requirements for managing CAPA during the certification and batch release process. The revision emphasizes robust CAPA procedures to ensure compliance with the updated guidelines.
4. WHO's Updated GMP Guidelines
The WHO has updated its GMP guidelines to incorporate more stringent requirements for CAPA, focusing on risk assessment and documentation. These updates aim to enhance global health and safety standards.
Conclusion
CAPA management is a critical component of pharmaceutical manufacturing, ensuring that issues are identified, investigated, and resolved in a controlled and systematic manner. By adhering to established guidelines such as ICH Q10, FDA 21 CFR Part 820, ISO 13485:2016, EU GMP Chapter 1, WHO GMP, and PIC/S GMP, pharmaceutical companies can maintain product quality, regulatory compliance, and operational efficiency. Implementing robust CAPA management processes and best practices is essential for achieving excellence in this highly regulated industry.