FDA Observations Complaint Management
Explore the top 7 FDA observations on complaint management in the pharma industry. Understand the root causes, corrective actions, and preventive measures to ensure compliance and improve quality.
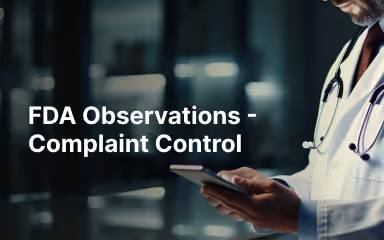
1. Inadequate Complaint Handling Procedures
Root Cause:
Lack of comprehensive procedures, insufficient training, inadequate trend analysis, failure to escalate complaints, and unclear third-party call center guidance.
Corrective Action:
Revise SOPs, implement robust training, enhance trend analysis, investigate recurring complaints, and provide guidelines for third-party call centers.
Preventive Action:
Establish continuous improvement, robust training, advanced analytical tools, maintain quality dashboard, and hold regular review meetings with third-party providers.
Reference FDA 483:
Company Name: Sun Pharmaceutical Industries Limited
Issue Date: 15-Dec-23
Inspection Dates: 04 Dec 2023 to 15 Dec 2023
Investigators: Pratik S Upadhyay
2. Inadequate Investigation of Unexplained Discrepancies
Root Cause:
Lack of microbial contamination assessment procedures, insufficient training, and unclear escalation criteria for complaint investigations.
Corrective Action:
Revise procedures for microbial assessment, train staff on new procedures, and introduce Quality Control review for microbial-related complaints.
Preventive Action:
Conduct routine audits, enhance complaint intake for microbial indicators, and periodically review microbial assessment criteria based on standards and guidance.
Reference FDA 483:
Company Name: Kilitch Healthcare India Limited
Issue Date: 20-Oct-23
Inspection Dates: 12 Oct 2023 to 20 Oct 2023
Investigators: Anastasia M Shields, Justin A Boyd
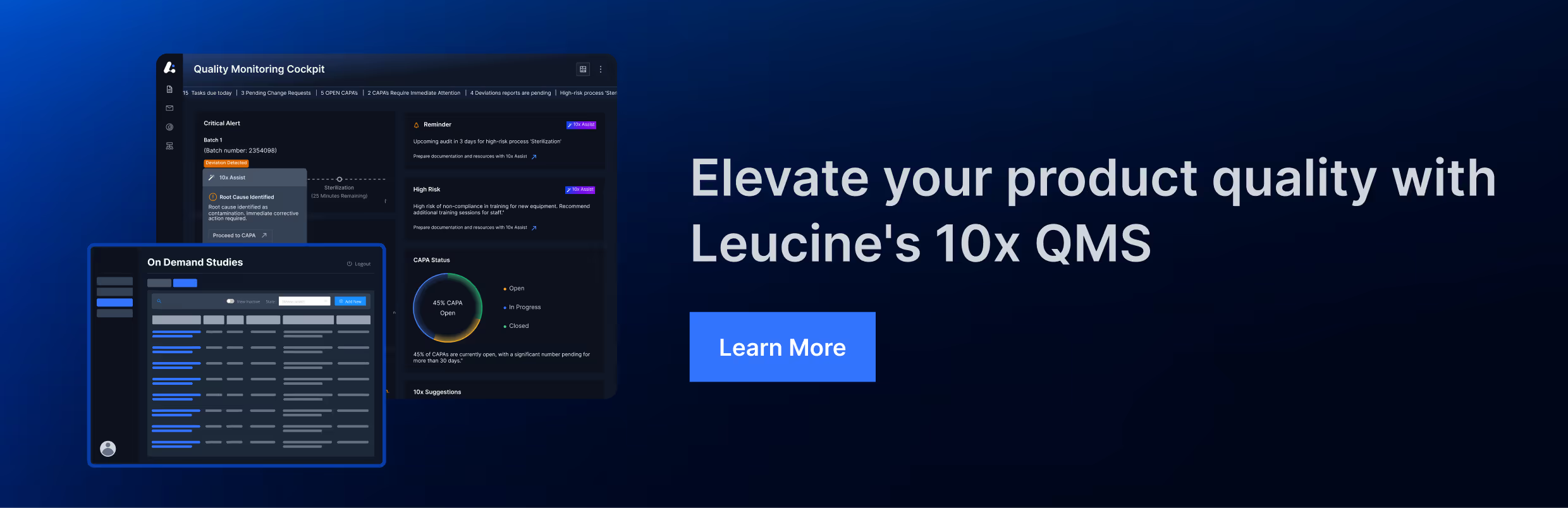
3. Deficient Complaint Procedures Impact Drug Safety Evaluation
Root Cause:
Lack of thorough complaint procedures, inefficient product testing, and insufficient employee training.
Corrective Action:
Revise complaint procedures, implement product testing, and train employees on updated procedures.
Preventive Action:
Periodically review complaint procedures, conduct regular training, and implement a tracking system for complaints and investigations.
Reference FDA 483:
Company Name: SCA Pharmaceuticals, LLC
Issue Date: 20-Oct-23
Inspection Dates: 18 Sep 2023 to 20 Oct 2023
Investigators: Jonah S Ufferfilge, John P Mistler
4. Missing Conclusions and Follow-Up in Discrepancy Records
Root Cause:
Unclear investigation procedures, insufficient training, inadequate documentation, and failure to extend investigations to impacted batches and critical processes.
Corrective Action:
Develop comprehensive SOPs, conduct thorough training, enhance record-keeping, and expand investigation scope to include impacted batches and equipment.
Preventive Action:
Regular training programs, periodic review by senior quality personnel, implement digital tracking, and adopt a risk-based approach for investigations.
Reference FDA 483:
Company Name: Sichuan Deebio Pharmaceutical Co. Ltd.
Issue Date: 08-Sep-23
Inspection Dates: 04 Sep 2023 to 08 Sep 2023
Investigators: Arsen Karapetyan, Anders W Evenson
5. Unreviewed Discrepancies and Batch Specification Issues
Root Cause:
Superficial investigations, lack of trained personnel, inadequate QMS, poor risk evaluation, delayed complaint responses, and insufficient environmental control.
Corrective Action:
Strengthen investigation procedures, review QMS, enhance training, implement escalation processes, expedite complaint handling, and upgrade environmental controls.
Preventive Action:
Ensure CAPA effectiveness, regular staff training, update SOPs, integrate risk management, and promote a culture of transparency in reporting quality issues.
Reference FDA 483:
Company Name: Central Admixture Pharmacy Services Inc
Issue Date: 25-Aug-23
Inspection Dates: 10 Jul 2023 to 25 Aug 2023
Investigators: Jolanna A Norton, Rachel C Stanton, Doan N Singh, Xiaohui Shen
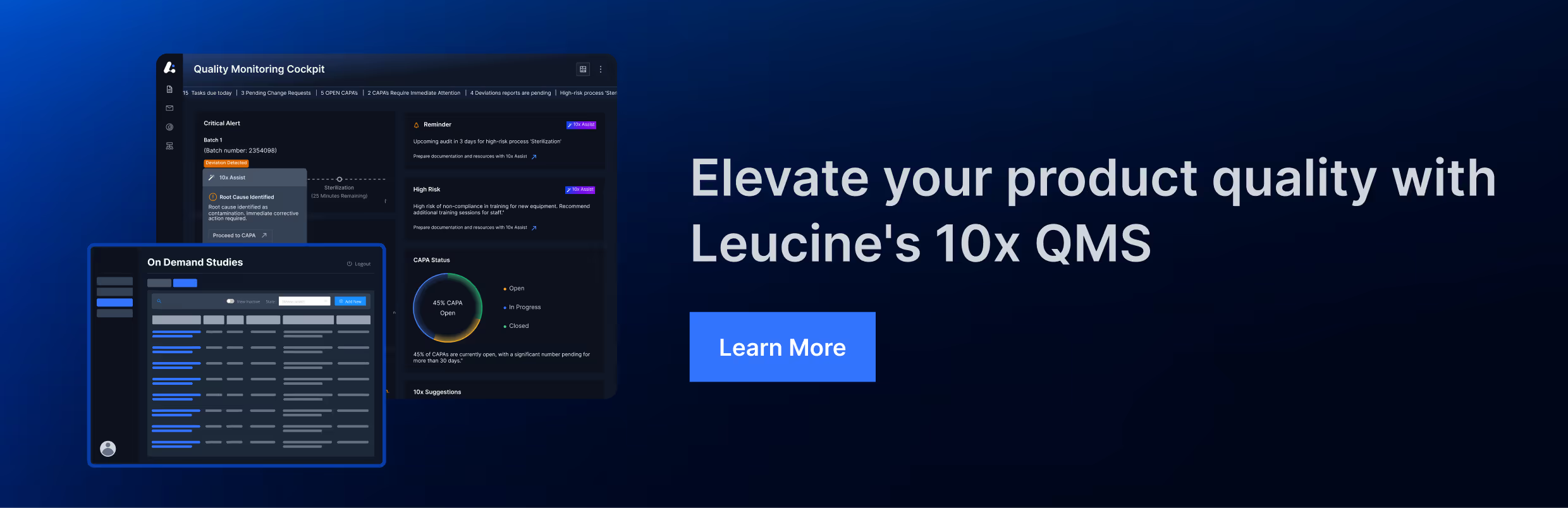
6. Missing Investigation Findings and Follow-Up in Records
Root Cause:
No standardized complaint investigation procedure, insufficient training, inadequate quality oversight, lack of trend analysis tools, and ineffective inter-departmental communication.
Corrective Action:
Revise SOPs for complaint handling, implement targeted training, establish quality oversight mechanisms, and enhance trend analysis technology.
Preventive Action:
Institute continuous training, upgrade IT systems for trend analysis, strengthen inter-departmental communication, and regularly review documentation processes in CAPA system.
Reference FDA 483:
Company Name: Novo Nordisk A/S
Issue Date: 04-May-23
Inspection Dates: 27 Apr 2023 to 04 May 2023
Investigators: Prabhu P Raju, Unnee Ranjan, Mikhail Ovanesov, Sergey Akimov
7. Inadequate Procedures for Managing Drug Complaints
Root Cause:
Undefined complaint handling procedures, lack of training, inadequate quality control oversight, and inefficient complaint tracking system.
Corrective Action:
Revise and document complaint procedures, implement comprehensive training, enhance quality control oversight, and upgrade the complaint tracking system.
Preventive Action:
Establish regular audits, periodically review complaint processes, implement feedback loops, and conduct regular training refreshers for staff.
Reference FDA 483:
Company Name: Cipla Limited
Issue Date: 17-Feb-23
Inspection Dates: 06 Feb 2023 to 17 Feb 2023
Investigators: Saleem A Akhtar, Jose E Melendez