The Need for Risk Assessment in Quality Management Systems (QMS) for Pharma
Understand risk management in pharma QMS for compliance and safety.
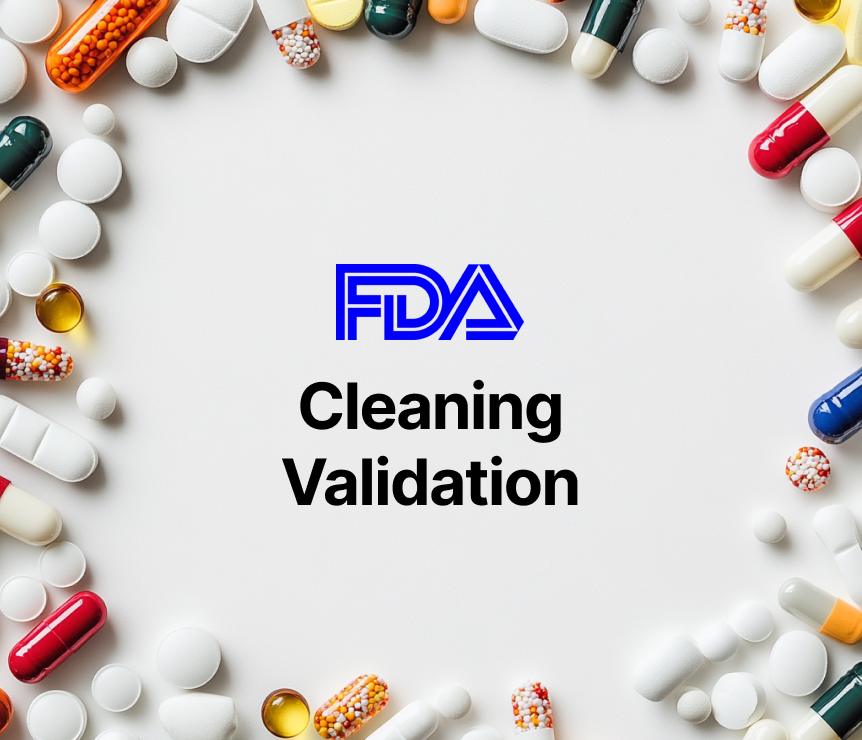
What is Risk Management in QMS?
Risk management in a Quality Management System involves identifying, assessing, and controlling risks that could potentially impact the quality of pharmaceutical products. The goal is to minimize the probability and impact of adverse events, ensuring compliance with regulatory requirements and maintaining patient safety within a pharmaceutical quality management system.
Risk management is a systematic process that includes risk identification, risk analysis, risk evaluation, risk control, and risk communication. It is a continuous process that should be integrated into all aspects of the QMS in pharma, from product development to manufacturing and distribution.
The Risk Management Process
- Risk Identification
- The first step in the risk management process is to identify potential risks. This involves a thorough examination of all processes, systems, and activities to pinpoint areas where risks could arise.
- Common methods for risk identification within a pharmaceutical quality management system include:
- Brainstorming sessions
- Checklists
- Reviewing historical data
- Risk Analysis
- Once risks have been identified, the next step is risk analysis. This involves assessing the likelihood and impact of each identified risk.
- Various tools and techniques can be used for risk analysis in a QMS in pharma, including:
- Failure Modes and Effects Analysis (FMEA)
- A systematic approach for evaluating processes to identify where and how they might fail and assessing the relative impact of different failures within a pharmaceutical quality management system.
- Hazard Analysis and Critical Control Points (HACCP)
- A preventive approach to food safety, which can be adapted for pharmaceutical processes to identify critical points where risks can be controlled within a QMS in pharma.
- Fault Tree Analysis (FTA)
- A top-down approach to identify potential causes of system failure.
- Failure Modes and Effects Analysis (FMEA)
- Risk Evaluation
- Risk evaluation involves comparing the estimated risks against established risk criteria to determine their significance. This helps prioritize risks, focusing resources on managing the most critical ones.
- Risks can be categorized into different levels (e.g., high, medium, low) based on their likelihood and impact within a pharma quality management system.
- Risk Control
- After evaluating the risks, the next step is to implement measures to control them. Risk control strategies can include various methods within a QMS in pharma:
- Risk Avoidance: Changing plans to avoid the risk entirely.
- Risk Reduction: Implementing actions to reduce the likelihood or impact of the risk.
- Risk Acceptance: Acknowledging the risk and deciding to accept it without further action.
- Risk Transfer: Shifting the risk to another party (e.g., through insurance).
- After evaluating the risks, the next step is to implement measures to control them. Risk control strategies can include various methods within a QMS in pharma:
- Risk Communication
- Effective risk communication ensures that all stakeholders are aware of the risks and the measures in place to manage them.
- This includes:
- Internal communication within the organization
- External communication with regulatory bodies, partners, and customers, as part of a comprehensive pharmaceutical quality management system.
- Risk Review
- Risk management is an ongoing process, essential for maintaining the integrity of a pharmaceutical quality management system (QMS in pharma).
- Regular management reviews are crucial to ensure that risk controls are effective and to identify any new risks that may arise.
- Continuous monitoring and periodic reassessment within the framework of what is the quality management system help maintain a proactive approach to managing potential issues.