Batch Record: A Detailed Guide on Batch Manufacturing & Electronic Batch Records
Learn how to optimize production with an essential guide to batch records. Discover best practices and improve efficiency in your processes. Read more!
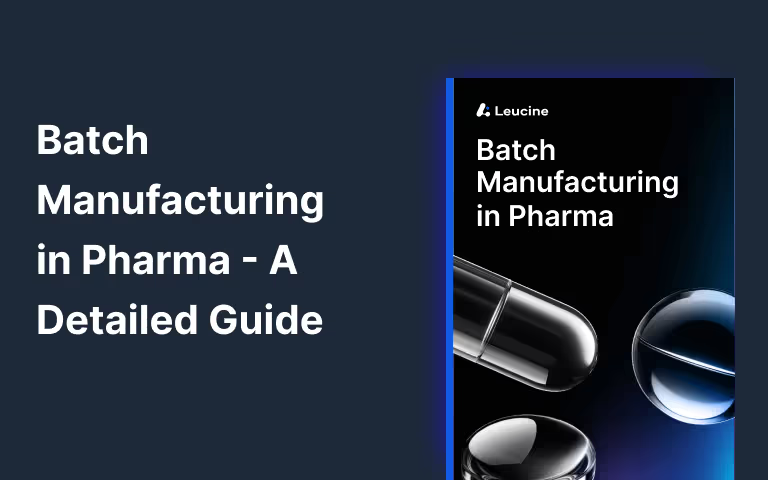
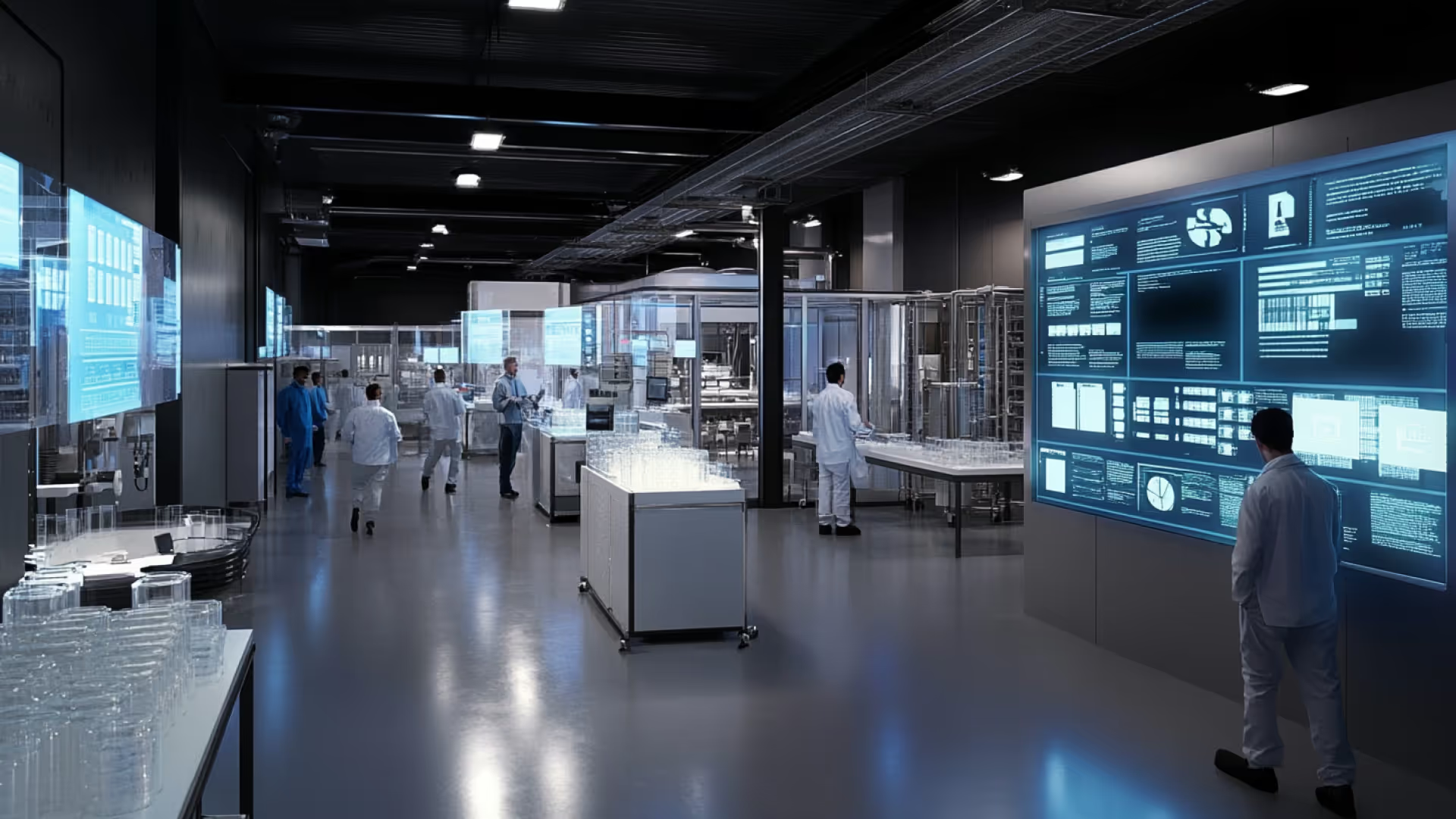
Introduction
Batch manufacturing is the backbone of pharmaceutical production, ensuring precision, consistency, and regulatory compliance. In an industry where quality control and traceability are paramount, the batch manufacturing process ensures products are manufactured consistently and meet safety and quality standards. Batch Manufacturing Records (BMRs) serve as the essential documentation that tracks every stage of the production process.
With increasing regulatory scrutiny, pharmaceutical companies are shifting from traditional paper-based records to Electronic Batch Records (EBRs) to enhance efficiency, accuracy, and compliance. This guide explores batch manufacturing, batch records, and the transformational benefits of transitioning to EBRs in modern pharmaceutical production.
Source : Pharmaceutical Batch Manufacturing Market Report
What is Batch Manufacturing?
Batch manufacturing is a structured production approach where drugs are produced in predefined batches, ensuring consistency and quality control. It aligns with current Good Manufacturing Practices (cGMP) and global compliance regulations, minimizing variability in drug production.
Market Insights: In 2021, the global pharmaceutical batch manufacturing market was valued at approximately $1.5 billion, with continued growth expected due to evolving regulatory requirements.
Understanding Batch Manufacturing Records (BMR)
A Batch Manufacturing Record (BMR)—also known as a Batch Production Record (BPR) or Master Batch Record (MBR)—is a comprehensive document that tracks the production details of a specific batch. It is crucial to document each stage of the batch process, from raw materials to equipment maintenance, to ensure traceability and safety throughout the manufacturing cycle.
Key Components of a BMR:
- Batch Manufacturing Instructions: Defines raw materials, quantities, and procedures to ensure consistency.
- Process Documentation: Records every stage of production, including equipment use, environmental conditions, and in-process tests.
- Traceability & Compliance: Tracks raw material origins, personnel involvement, and equipment used—critical for recalls and quality investigations.
Other types of Batch Records in Pharmaceuticals
Pharmaceutical manufacturing relies on various batch records to ensure compliance and product quality. Batch production records are crucial in ensuring accuracy and compliance during the manufacturing process.
1. Master Batch Record (MBR)
A standardized document that outlines the entire manufacturing process, including raw materials, equipment, and quality control protocols, is known as master batch records.
2. Batch Production Record (BPR)
Created for each batch, detailing equipment settings, raw material usage, and processing steps to ensure adherence to the MBR.
3. Electronic Batch Record (EBR)
A digital version of batch records that enhances data integrity, real-time tracking, and compliance by automating documentation.
4. Packaging Batch Record (PBR)
Documents packaging batch records to maintain consistency and compliance by detailing packaging materials, labeling instructions, and packaging line setup.
5. Cleaning Batch Record (CBR)
Ensures equipment and facilities are cleaned properly after each batch to prevent contamination.
6. Validation Batch Record (VBR)
Used during process validation to confirm the manufacturing process meets regulatory requirements.
7. Stability Batch Record (SBR)
Tracks stability testing, ensuring drug safety and effectiveness throughout its shelf life.
8. Investigational New Drug (IND) Batch Record
Maintains compliance in clinical trials, documenting investigational drug production and testing.
Relation between Good Manufacturing Practices (GMP) and Batch Records
While Good Manufacturing Practices (GMP) are essential regulations that ensure the quality, safety, and consistency of pharmaceutical products, Batch Records play a crucial role in GMP compliance by providing a detailed and accurate record of each stage of the manufacturing process.
Maintaining detailed Batch Records is necessary for ensuring regulatory compliance within the pharmaceutical industry.
To comply with GMP regulations, Batch Records must document:
- Raw Materials: Includes supplier details, batch numbers, and quality control tests to ensure traceability and product integrity.
- Production Process: Records equipment settings, processing steps, and any deviations from standard procedures to ensure batch consistency.
- Quality Control Tests: Captures test results, ensuring that each batch meets regulatory quality standards before release.
- Packaging Process: Documents packaging materials, labeling instructions, and line setup to maintain product safety and compliance.
Maintaining detailed and accurate batch records is critical for GMP compliance, ensuring product quality, regulatory adherence, and patient safety.
Difference between Batch Formula Record (BFR), Master Formula Record, and Batch Manufacturing Record
Understanding the difference between Batch Formula Record, Master Formula Record and Batch Manufacturing Record is crucial for pharmaceutical manufacturing. These records ensure batch consistency, compliance, and quality control, but they serve different purposes in production process.
- Master Formula Record (MFR): A standardized document serving as a reference for multiple batch productions, ensuring consistency across all batches.
- Batch Formula Record (BFR): Specifies exact ingredient quantities and processing steps for a single batch, derived from the MFR.
- Batch Manufacturing Record (BMR): A comprehensive document that tracks every step of production for a specific batch, including raw materials, processing, and quality control.
Transitioning to Electronic Batch Records (EBRs)
Historically, pharmaceutical companies relied on manual paper-based batch records, which were time-consuming, error-prone, and inefficient. However, the industry is now shifting towards Electronic Batch Records (EBRs)—a digital transformation that is enhancing efficiency, accuracy, and regulatory compliance.
Why is this shift important?
- Reduces Human Errors: Digital records minimize data entry mistakes and ensure real-time accuracy.
- Enhances Compliance: Automated audit trails and instant reporting make regulatory inspections easier.
- Boosts Efficiency: Eliminates delays in batch release, cutting processing times by up to 50%.
- Improves Data Integrity: Adheres to FDA 21 CFR Part 11 guidelines for electronic recordkeeping.
Pharmaceutical manufacturers looking to optimize batch execution must adopt digital batch records for enhanced compliance and efficiency.
This guide explores batch manufacturing, batch records, and the significance of transitioning to EBRs in modern pharmaceutical production.
Batch Processing in Manufacturing
Batch processing ensures controlled production by meticulously tracking and verifying the steps involved in the production processes of each specific batch of products, allowing for:
- Quality Control: Each batch undergoes rigorous testing before distribution.
- Production Flexibility: Manufacturers can efficiently produce multiple formulations within the same facility.
- Cost Optimization: Reduces waste and resource usage, improving operational efficiency.
📊 Survey Insight: 65% of pharmaceutical manufacturers prefer batch processing for its flexibility in handling multiple product types.
The Importance of Batch Manufacturing Records in Quality Control
Batch Manufaturing Records play a crucial role in ensuring product quality and regulatory compliance. They support:
- Regulatory Compliance: Required by FDA, EMA, and GMP guidelines.
- Recall Management: Enables traceability in case of product recalls.
- Continuous Improvement: Helps identify process inefficiencies and enhance quality.
Batch Manufacturing Record Guidelines
- Good Manufacturing Practices (GMP): Governs validation, documentation, and personnel training. The documentation process is crucial for enhancing operational efficiency and data integrity within manufacturing.
- Batch Records Documentation: Ensures traceability and compliance.
- Quality Control Measures: Includes sampling, testing, and release protocols.
Read more about Batch Manufacturing Guidelines
Audit Readiness Checklist
To ensure compliance with cGMP and regulatory audits, use a batch manufacturing audit checklist, covering:
- Documentation accuracy & completeness
- Personnel training verification
- Equipment maintenance records
- Batch release procedures
FDA Observations & Compliance
2024 Insight: 35% of FDA 483 observations cited inadequate batch record documentation as a major compliance issue.
How EBRs Improve Compliance:
- Reduces documentation errors
- Enhances traceability & audit readiness
- Ensures real-time regulatory adherence
Solution: Implement EBRs to prevent regulatory risks and improve compliance efficiency.
Expert Insights: The Long-Term Benefits of MES
Implementing a Manufacturing Execution System (MES) can be challenging, especially for mid-sized companies concerned about costs and infrastructure. In a detailed podcast, Vilas Dholye, former executive at Cipla and Dr. Reddy’s, discusses how focusing on the long-term benefits of MES—such as enhanced data integrity and reduced variability—can help overcome these hurdles. Key takeaways include:
- Data Integrity: MES reduces manual errors, ensuring more accurate and reliable data.
- Process Consistency: Standardizes operations, leading to consistent product quality.
- Regulatory Compliance: Simplifies adherence to regulatory standards through automated documentation.
Listen to the full discussion to gain deeper insights. → MES Implementation in Pharma: Lessons from Vilas Dholye
Conclusion
Batch Manufacturing Records—whether paper-based or electronic (EBRs)—are indispensable in pharmaceutical manufacturing. The transition to EBRs is driving efficiency, compliance, and competitive advantage in the industry.
Leucine’s Paperless Batch Execution streamlines production with:
- 60% faster documentation
- 70% improved SOP adherence
- Faster deviation resolution
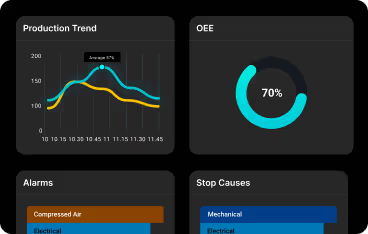
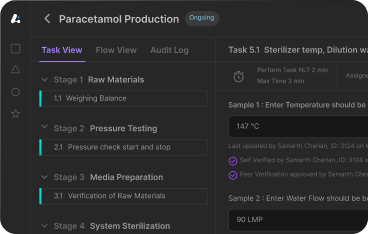

View and learn more about Cleaning Validation with our comprehensive list of resources